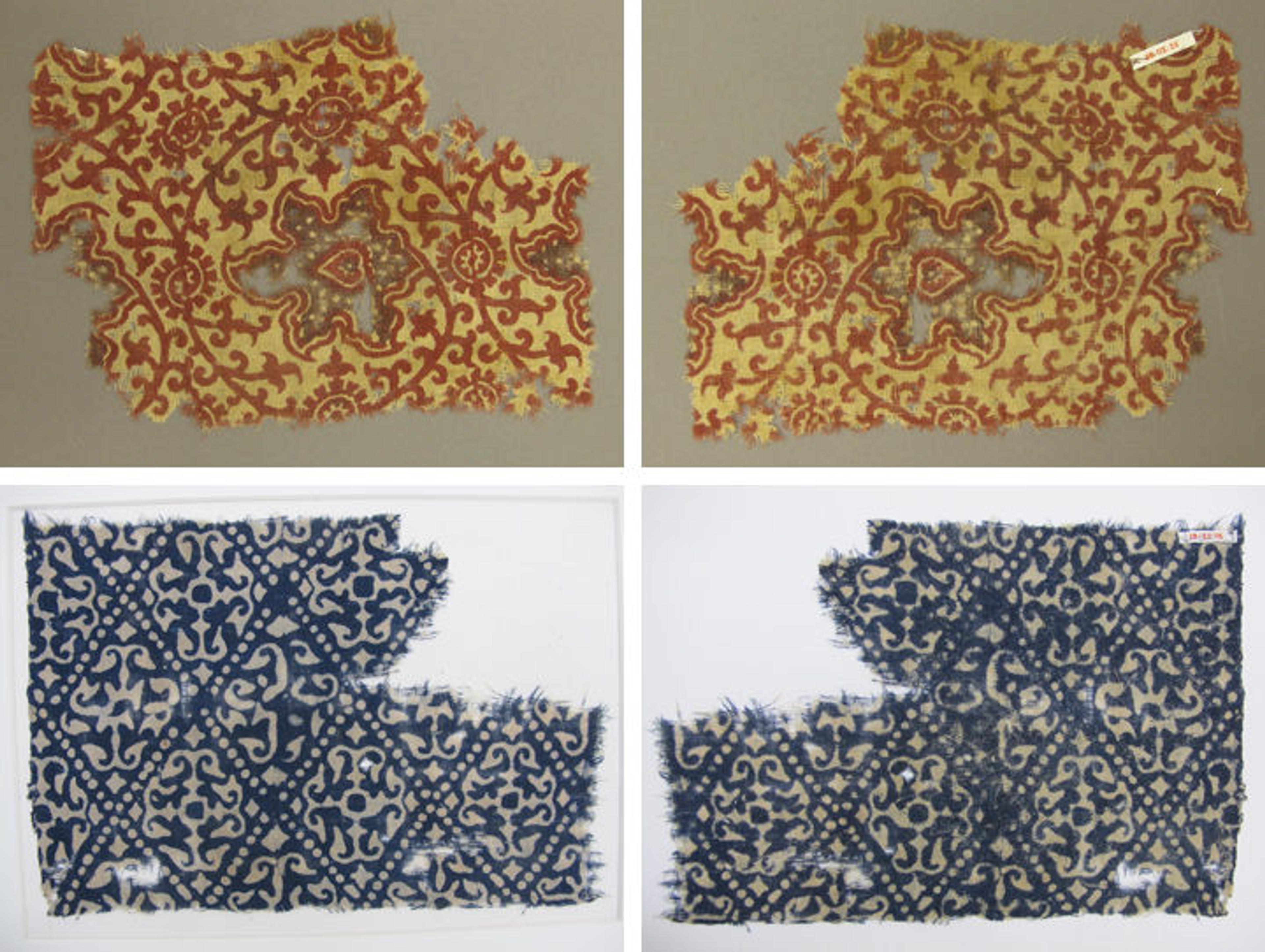
Top: Fig. 1a, b. Fragment (front [left], reverse [right]), 13th–14th century. Attributed to India; Found Fustat, Egypt. Cotton; block-printed and mordant-dyed, 8.5 in. high 6.00 in. wide (21.6 cm high 15.2 cm wide). The Metropolitan Museum of Art, New York, Purchase, V. Everit Macy Gift, 1930 (30.112.25). Bottom: Fig. 2a, b. Fragment (front [left], reverse [right]), 13th–14th century. Attributed to India. Islamic. Cotton; block-printed and resist-dyed, 6.62 in. high 10.00 in. wide (16.8 cm high 25.4 cm wide). The Metropolitan Museum of Art, New York, Purchase, V. Everit Macy Gift, 1930 (30.112.41)
«Two Islamic textile fragments made of hand-spun and handwoven cotton are featured in the exhibition Jerusalem 1000–1400: Every People Under Heaven, on view through January 8, 2017 (figs. 1a, b; 2a, b). Both display a monochromatic color scheme on undyed cotton fabric, one with a red pattern, the other blue. These simple fragments are believed to be utilitarian rather than luxury items, exemplifying an ancient block printing tradition and manifesting evidence of early global trade. Historically, Indian textile production has been acclaimed worldwide for the alchemy of applying natural dyes to cotton fabric—a difficult fiber to dye—and for the resulting vivid and fast colors. Both in the past and up to the present day, Indian artisans have been known for their skillful and ingenious use of local materials to produce exquisite textiles.»
After studying and preparing the two textiles for Jerusalem 1000–1400, I realized that India still retains a lively textile-producing cottage industry, which lead me to formulate research trips supported by Met Travel Grants. My plan was to study and document current production methods of block-printed, tie-dyed, and painted textiles (also known as resist-dyed). The historic Indian block prints are ascribed to workshops of Gujarat, where a substantial printing tradition still exists. Studying the current practices is beneficial to understanding the evolution of this heritage and may lead to deeper insights of how the historic textiles were produced.
The two Indian block prints at The Met are part of a group of early Islamic textiles, also known as the Fustat (Fostat) group, Indo-Egyptian, and Egypto-Arabic textiles, depending on the prevailing understanding of their provenance. The two fragments are representative of The Met's small collection of about 20 textiles from this esteemed group. They were purchased in 1930 by a well-known curator of Islamic Art at The Met, Maurice Dimand, during a trip to the near east. Their early provenance before arriving to The Met is unsubstantiated, but can be surmised.
Textiles from the Indian block-printed group came to light in the 1920s in Fustat (Old Cairo), Egypt, and were collected rather than excavated professionally, making them difficult to date. Fortunately, more recent controlled archeological excavations, including finds of textiles similar in construction and pattern, were found at Quseir al-Qadim in Egypt, and were assigned to the Mamluk period (mid-13th–late 14th century). The two Met fragments are attributed to the 13th to 14th century. Recent studies highlight the early provenance of the block prints and their popularity and commercial value over a prolonged time period.
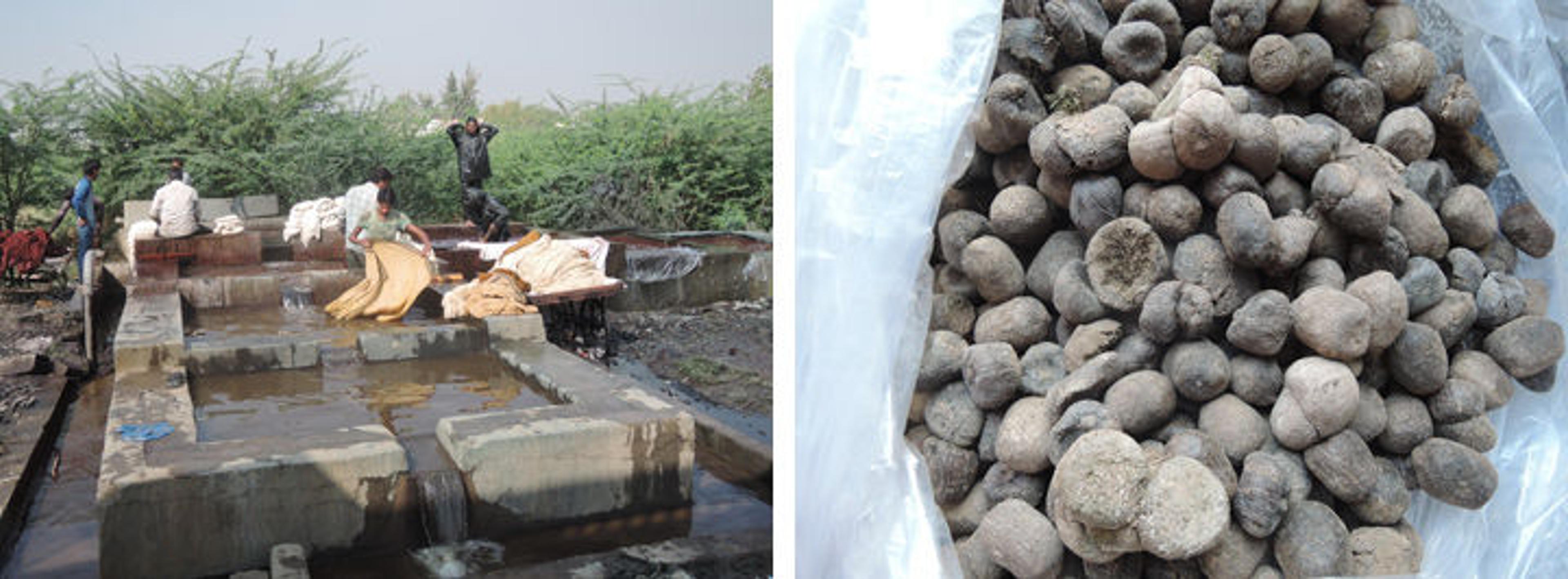
Left: Fig. 3. A group of Dhobi (belonging to caste of washers) using progressively declining pools for washing fabric, Ajrakhpur, Kutch, Gujarat, 2016. Right: Fig. 4. A bag of camel dung, before treatment, Ajrakhpur, Kutch, Gujarat, at the workshop of Sufiyan Khatri, 2016. Photos by Yael Rosenfield
The first steps of the current production process involved in the creation of the block-printed textiles require long and laborious cleaning and bleaching of the cotton fabric to remove impurities and prepare the fiber to receive the dye (fig. 3). The fabric is immersed in a solution of camel dung, castor oil, soda ash, and water, and then subjected to trampling and beating until a soap-like solution is formed (fig. 4). This treatment is repeated several times, interspersed with laying in the sun to be bleached by oxidation. In India, it is common to see fields strewn with lengths of fabric laid on the ground to dry and bask in the sun (fig. 5).
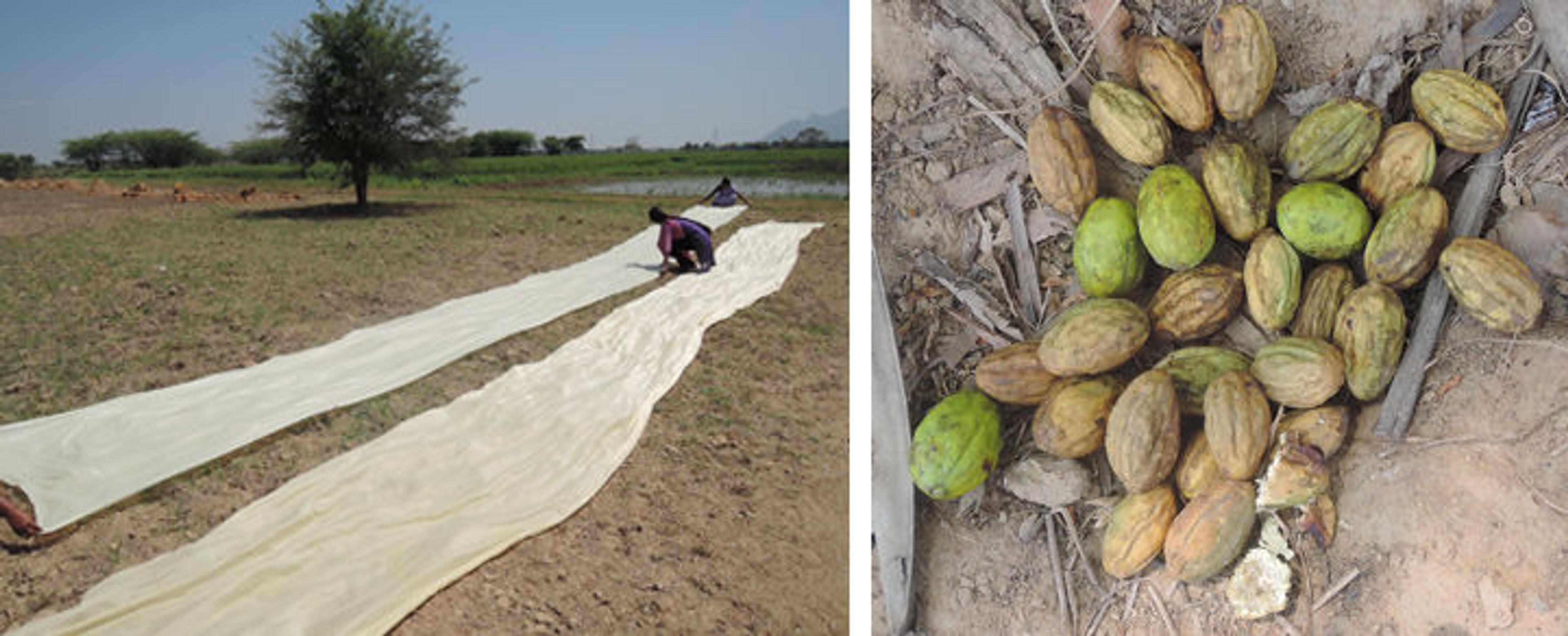
Left: Fig. 5. Lengths of fabric drying in the sun, Sri Kalahasti, Andhra Pradesh, 2016. Right: Fig. 6. A handful of myrobalan, Sri Kalahasti, Andhra Pradesh, 2016, both photos from the workshop of Mr. Niranjan. Photos by Yael Rosenfield
A mordant is used in order to fix the dye molecule to the cotton fiber, which also influences the hue, intensity, and colorfastness of the end result. Myrobalan (Harde), a strong tannin from the fruit of Chebulic Myrobalan, a flowering evergreen tree, has traditionally been used as a mordant in India (fig. 6). It is applied to the fabric in a similar process to the one described above for the camel dung and is a precursor to the dyeing procedures.
The two Met fragments stand out for their distinctive patterning, which is associated with the block printing used in their creation. In fact, close inspection of the fragments reveals the footprint and size of the block. The red and blue fragments differ in their production due to the dyes used and their chemical properties: the red fragment was mordant-dyed, as opposed to the blue, which was resist-dyed. The red printed fabric was block printed with a paste of the mordant alum, which fixes the red dye to the cotton fiber, but only in the areas where it was applied (fig. 7a, b).
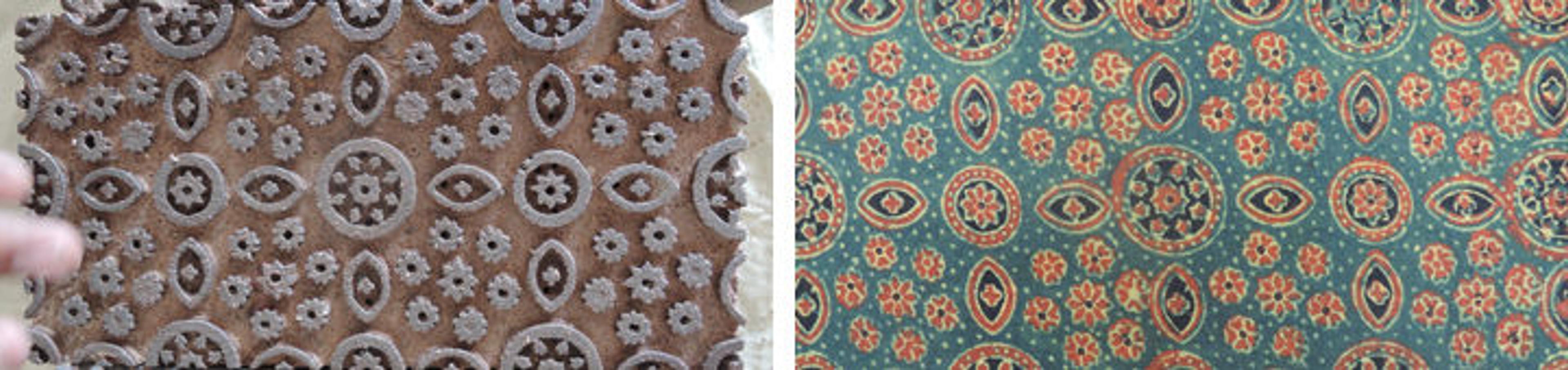
Left: Fig. 7a. A carved block for alum paste, Kutch, Gujarat, 2016. Right: Fig. 7b. A view of a printed Ajrakh fabric, Kutch, Gujarat, 2016. Both photos from the workshop of Sufiyan Khatri. Photos by Yael Rosenfield
The fabric was then immersed in a heated red dye bath until the desired red was achieved (fig. 8a, b). The darker shade of purple at the center of the leaves was block printed with a paste of iron acetate made of fermented scrap iron, which together with the myrobalan tannin created the corrosive dye that caused fiber loss.
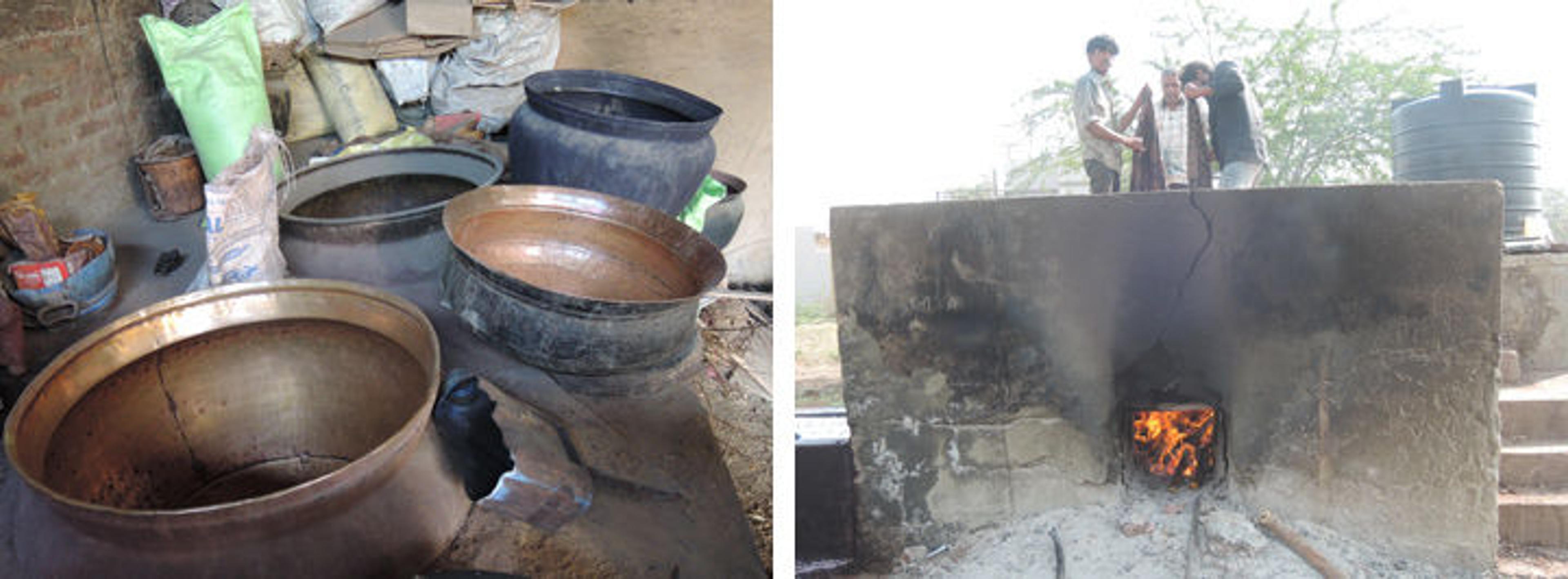
Fig. 8a, b. Copper pots such as these are traditionally used for dyeing red, Titanwala, Bagru, 2015 (left); A group of men red dyeing fabric in a heated red dye bath, Ajrakhpur, Kutch, Gujarat, 2016 (right). Photos by Yael Rosenfield
Traditionally, the red dye sourced and used in India has been madder from the Rubiaceae botanical family, growing in different locales. These plants include some of the following varieties: Indian mulberry (Morinda citrifolia L.), also known as Al; Indian madder or munjeet (Rubia cordifolia); and chay root (Oldenlandia umbellata L.). These dyes are all chemically different from each other and from the more well-known dyer's madder (Rubia tinctorum L.), which is Middle Eastern and European in origin. Analyzing the dyes used on historic textiles can therefore facilitate historical and geographic attribution.
Nobuko Shibayama, associate research scientist in the Department of Scientific Research, analyzed the red dye on five Indian block prints from The Met collection (30.112.23; 30.112.25; 30.112.29, 30.112.30; 30.112.33) using a high-performance liquid chromatography-photodiode array detector, and the results demonstrated that Al (Morinda citrifolia L.) was used on four textiles, one of which is of the two fragments featured in Jerusalem 1000–1400. This result was expected, as the Al shrub grew in Gujarat and this dye has been detected in other textiles from this group at other institutions. Dyer's madder (Rubia tinctorum L.) was found on one textile with a very saturated red, which raises the question of the source of the dye: Was it imported or grown locally?
Yet another fragment, a painted and printed textile, revealed the presence of chay root associated with the production of painted textiles along the Coromandel Coast. This preliminary study is inconclusive due to the small number of textiles analyzed, but research is ongoing. In India today, most artisans often use synthetic alizarin—an orange or red crystalline compound—though a discerning customer sometimes requests both Al and munjeet. Chay root has been discontinued and the knowledge of its application seems to be lost.
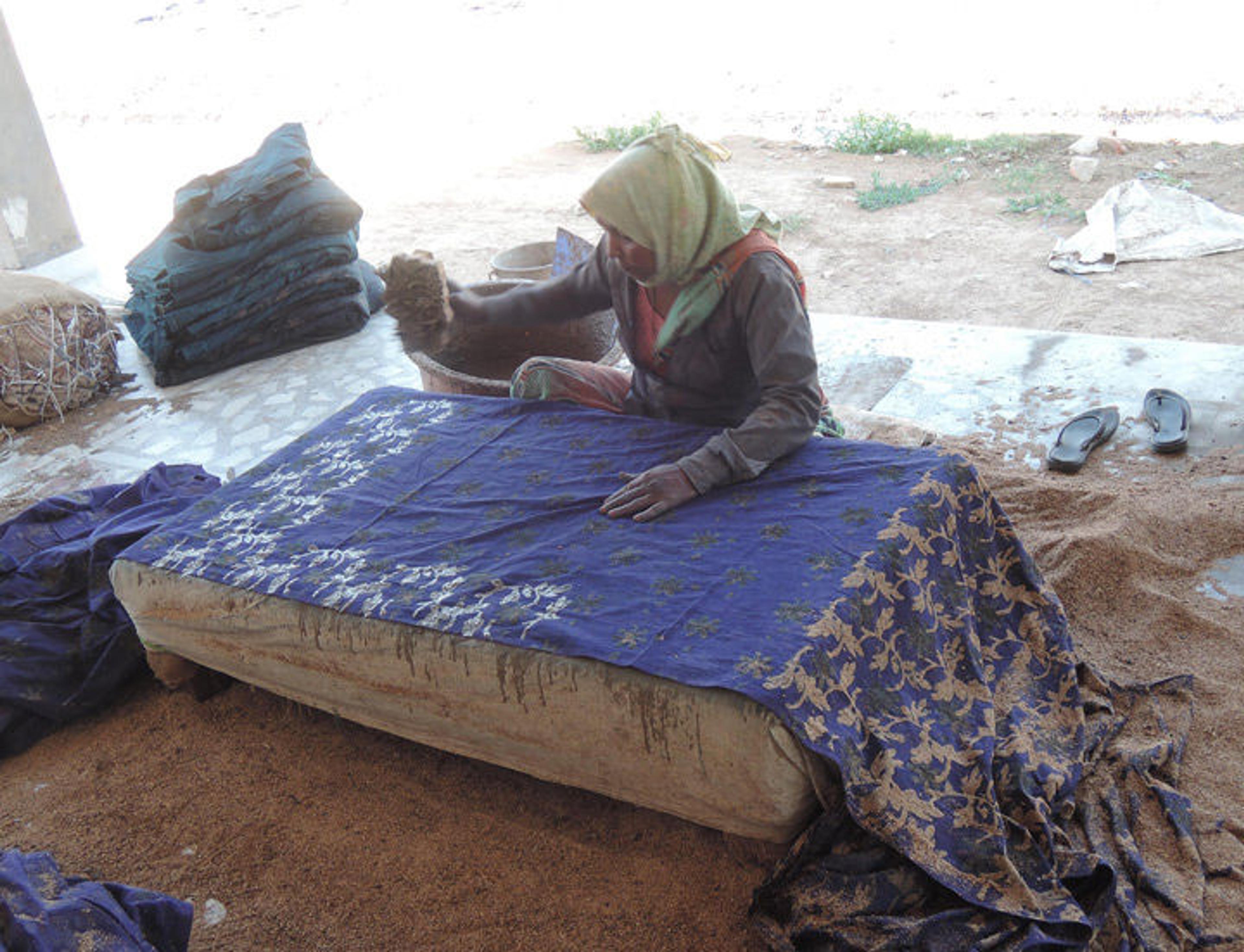
Fig. 9. A woman printing mud resist on indigo dyed fabric on a traditional low table, Titanwala workshop, Bagru, 2016. Photo by Yael Rosenfield
The patterning for the blue fragment was created by block printing a resist to the areas designated to remain undyed (fig. 9). The most common resist used for indigo today is a mud paste called Dabu, which often displays the characteristic "crack" lines where the dye penetrated the cracks in the resist (fig. 10a, b). After printing the resist, the fabric is immersed in the natural indigo dye vat (fig. 11). Then, when the fabric is exposed to air, the dye oxidizes to the insoluble blue form, adhering to the fibers permanently.
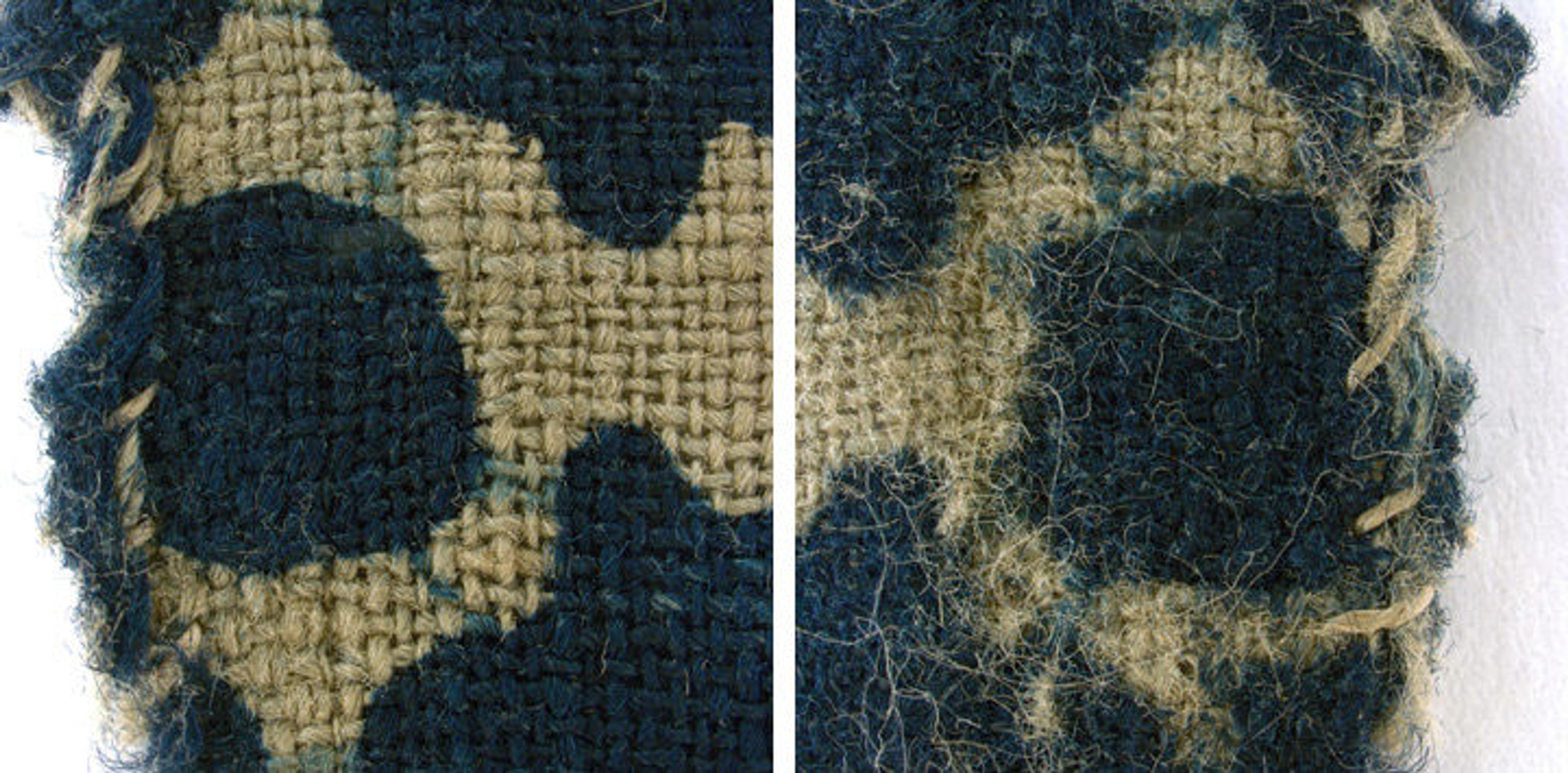
Fig. 10a, b. A detail of the blue fragment featured in Jerusalem 1000–1400 showing "cracks" in the resisted areas (front [left], reverse [right]), macro-photography, 10x. Photos by Yael Rosenfield
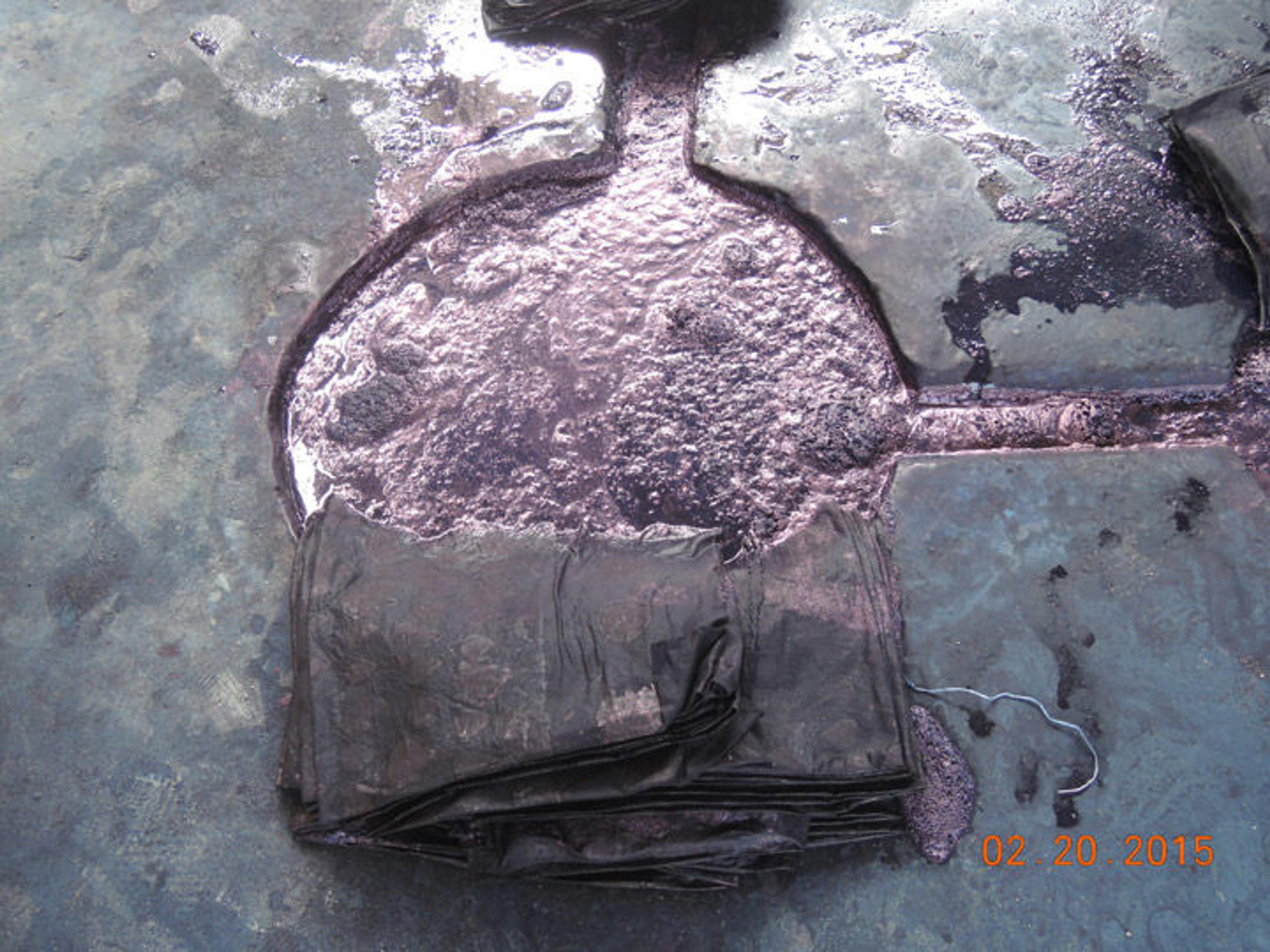
Fig. 11. Fabric submerged in an indigo vat, Akola, Rajasthan, 2015. Photo by Yael Rosenfield
It is remarkable that traditional textile-making processes are extant and prevalent in India today. The evolution of the historic methods is evident, with some ancient techniques still followed rigorously and others changing significantly. The most critical change is the dyes used, which are more often the synthesized chemical versions of alizarin and indigo, but surprisingly they are utilized in the complex time-honored processes such as those performed on the two Met fragments.
Acknowledgments
I would like to thank the Indian artisans who generously shared their knowledge:
Dr. Ismail and Sufiyan Khatri workshop, Kutch, Gujarat
Ramkishore Chhipa Derawala workshop, Bagru, Rajasthan
S. N. Titanwala workshop, Bagru, Rajasthan
J. Niranjan workshop, Sri Kalahasti, Andhra Pradesh
Related Links
Jerusalem 1000–1400: Every People Under Heaven, on view at The Met Fifth Avenue through January 8, 2017