Events
In addition to internal programming for The Met staff, we regularly host public lectures and presentations by specialists from outside the Museum.
Tauba Auerbach's Altar/Engine: A Case Study in Reconceptualizing Materiality
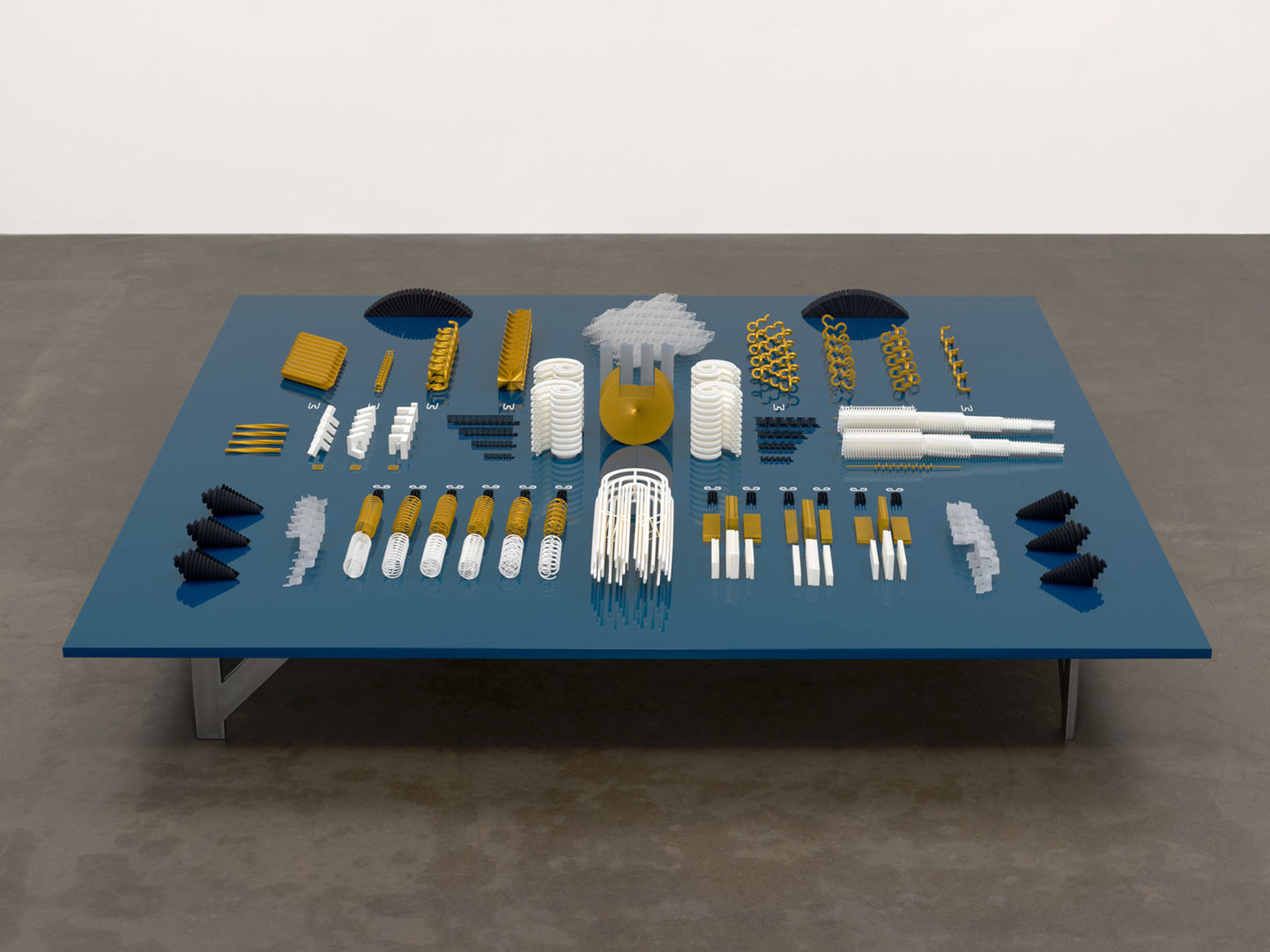
Tauba Auerbach (American, b. 1981). Altar/Engine, 2015. 3D-printed nylon and plastic on table of aluminum, wood, and paint; 116 parts ranging from 18 x 18 x 10 in. (45.7 x 45.7 x 25.4 cm) to 1 x 1 x 2 in. (2.5 x 2.5 x 5.1 cm), table 15 x 108 x 108 in. (38.1 x 274.3 x 274.3 cm). The Museum of Modern Art, New York (1336.2016.a-ddd). © Tauba Auerbach. Courtesy Paula Cooper Gallery, New York
Tuesday, November 27, 2018
3:30pm: Coffee reception
4 pm: Presentation
The Met Fifth Avenue - Bonnie J. Sacerdote Lecture Hall
Featuring Megan Randall, Assistant Projects Conservator, and Peter Oleksik, Associate Media Conservator, The Museum of Modern Art
On December 12, 2016, the Museum of Modern Art acquired Tauba Auerbach's 2015 work Altar/Engine. The work consists of seventy-six Rhino files 3D printed into individual plastic components of various types, resins, and finishes that are subsequently installed in a specific pattern on a nine-foot square highly finished painted aluminum platform and stainless steel base. It quickly became apparent to the artist and MoMA staff that in the short time since its creation, many of the material aspects had changed in significant and unacceptable ways. This paper will examine the steps the artist and MoMA took to ensure the work met the desired standards of the artist which resulted in a collective redefinition of its materiality. This redefinition, or reconceptualization, impacts its treatment, display, and long-term care.
Fifteen of the seventy-six 3D printed components significantly changed since their 2015 creation and were subsequently reprinted by the artist after acquisition. Changes were primarily indicated by breaks in the 3D printed structures or in deformation of coiled forms. The components are printed in four distinct visual types: white, black, frosted clear, and gold. The components in need of reprinting were the white, frosted clear, and painted gold types. This process revealed necessary changes in aspects of the printing process from the resin to the printing company that resulted in alterations to the texture and appearance of the components. Although accepted and approved by the artist, these changes led to a dialogue with the artist to develop MoMA's understanding of the artist's parameters of visual and material acceptance as well as a protocol for caring for the work moving forward.
The goal of these initial reprinting efforts was to increase the stability of the components for long term storage and display. However, their complexity and fragile nature will likely necessitate future printing by the artist and/or MoMA. This brings up larger questions of the relationship of the Rhino files with their 3D physical counterparts and where the work's fundamental materiality is located. Changes in files, software obsolescence, upgrades in printing and polymer technology can all drastically impact a work depending on the definition of its materiality.
As contemporary artists are gravitating to new materials and methods, this case study will illustrate MoMA's examination of the relatively nascent method of 3D printing. Combining expertise from various disciplines of conservation, namely sculpture, media, and science, MoMA is developing its approach to the long term care of 3D-printed material. This strategy considers its evolving status both in the artist's practice as well as mutable objects in the collection, touching on issues of maintenance, storage, and travel. This paper will also explore the possibility of refabricating components in the future, while addressing the likelihood of changing technologies with regards to the media files, the printing process, and polymer technology.