Unravelling the Hidden Production History of Sgraffito Ware from Nishapur
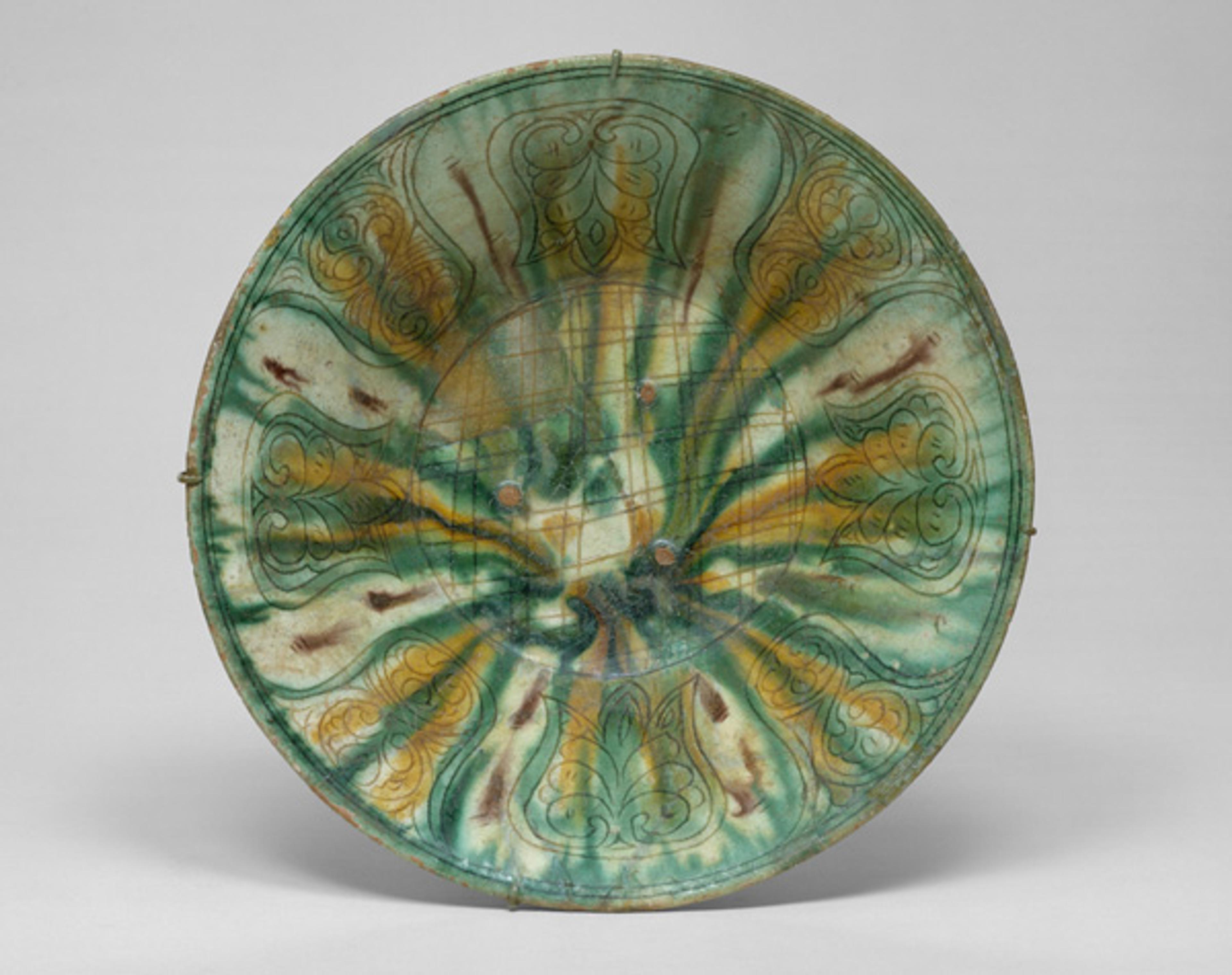
Bowl with green, yellow, and brown splashed decoration, 10th century. Iran, Nishapur. Islamic. Earthenware; white slip, incised and splashed with polychrome glazes under transparent glaze (sgraffito ware); H. 2 7/8 in. (7.3 cm), Diam. 10 1/4 in. (26 cm). The Metropolitan Museum of Art, New York, Rogers Fund, 1938 (38.40.137)
«Two years ago, during my time as a visiting scholar in the Met's Department of Scientific Research, I took advantage of the opportunity to spend time in the Museum's galleries. I had been particularly fascinated by the small but extremely interesting gallery dedicated to the archaeological excavation of Nishapur, Iran (gallery 452), the objects of which were of high aesthetic quality and displayed incredibly skillful craftsmanship.»
The collection is rather unique because the Metropolitan Museum excavated the site in the mid-1930s and 1940s, when the Iranian expedition brought to light the ruins of this important ancient town. Charles W. Wilkinson, then-curator of Near Eastern Art and head of the expedition, classified twelve ware groups (fig. 1), the majority of them undoubtedly produced by the ceramic kilns discovered not far from the ancient town itself.
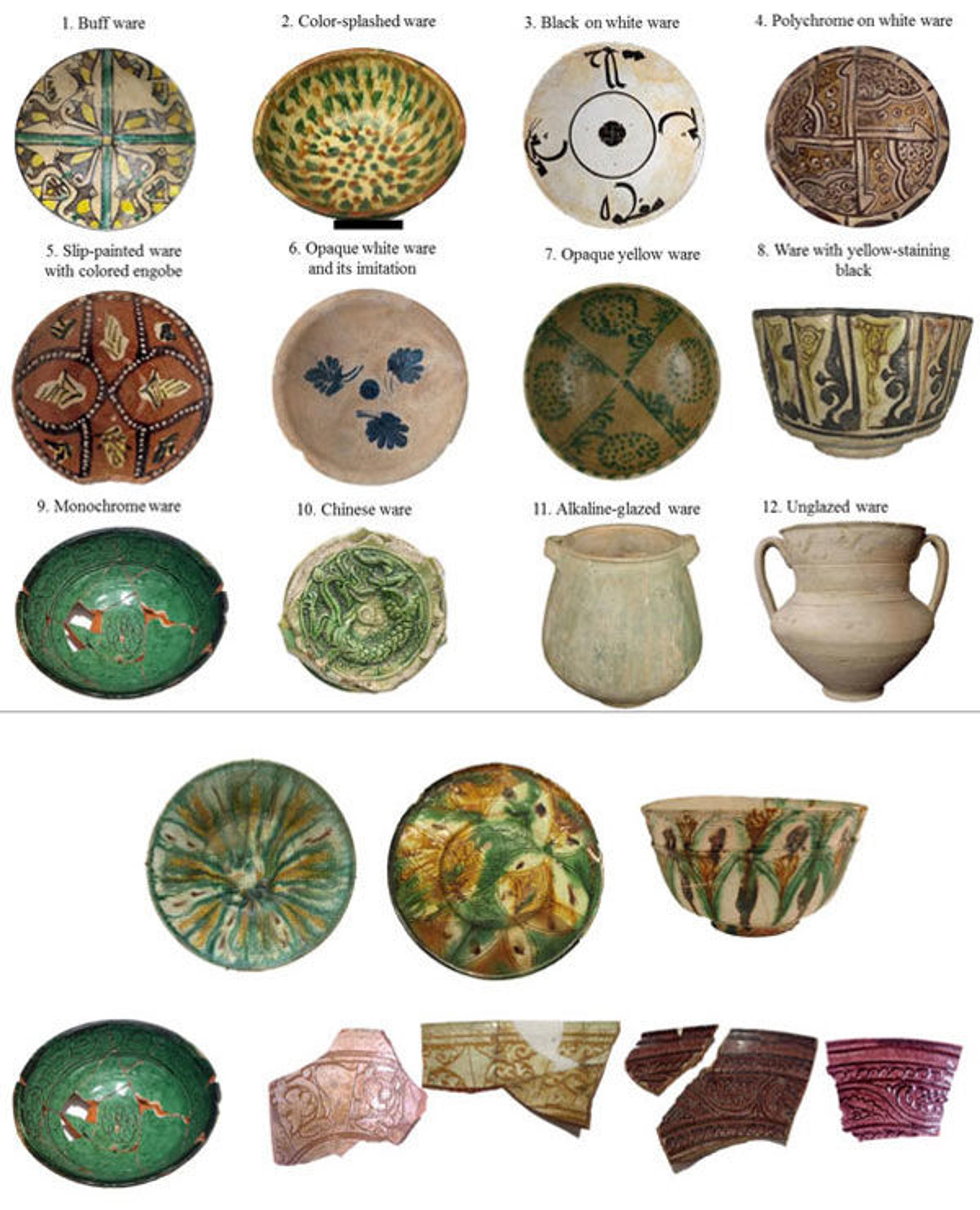
Fig. 1. Top: Examples of Charles W. Wilkonson's twelve pottery classifications. Bottom: Examples of sgraffito wares from Wilkinson's second and ninth classifications that were objects of this study
After returning to the Met this past year, this time as a Conservation and Scientific Research Fellow, I had the opportunity to actually put my hands on this sgraffito pottery. Sgraffito evolved in the tenth century from slipped glazed wares with color splashes, but its origin is still debated among scholars. Derived from an Italian term that means "scratched," sgraffito refers to the technique used to design the decorations.
Given the position of Nishapur on the network of the Silk Road that connected the central Islamic lands and Iran, the local earthenware production may give significant insights into the wider debate of the development of sgraffito production. My research was the first attempt to systematically characterize the nature of the materials employed in the production of Nishapur sgraffito wares, their production technology and provenance, by means of sophisticated scientific equipment.
The ceramic production technology is, in fact, one of the most intriguing aspects in ceramological studies: the reconstruction of how and when pottery was made, which materials were used, and where the materials were taken are top-priority questions for archaeologists. There is a scientific branch that aims to revealing these hidden aspects of ancient artifacts, archaeometry, the main goal of which is to analyze the objects by using a variety of analytical techniques and a broad range of tools—from simple microscopes to the sophisticated and cutting-edge instruments that are available in the Department of Scientific Research. Some of them can be run directly on the objects' surfaces without compromising their current status, but other kinds of scientific analyses require a sample taking.
The main challenge of archaeometry is finding ways to take the smallest samples possible without losing the possibility to perform all the analyses needed (fig. 2). Different techniques allowed me to reconstruct the production details and phases of the Nishapur sgraffito wares.
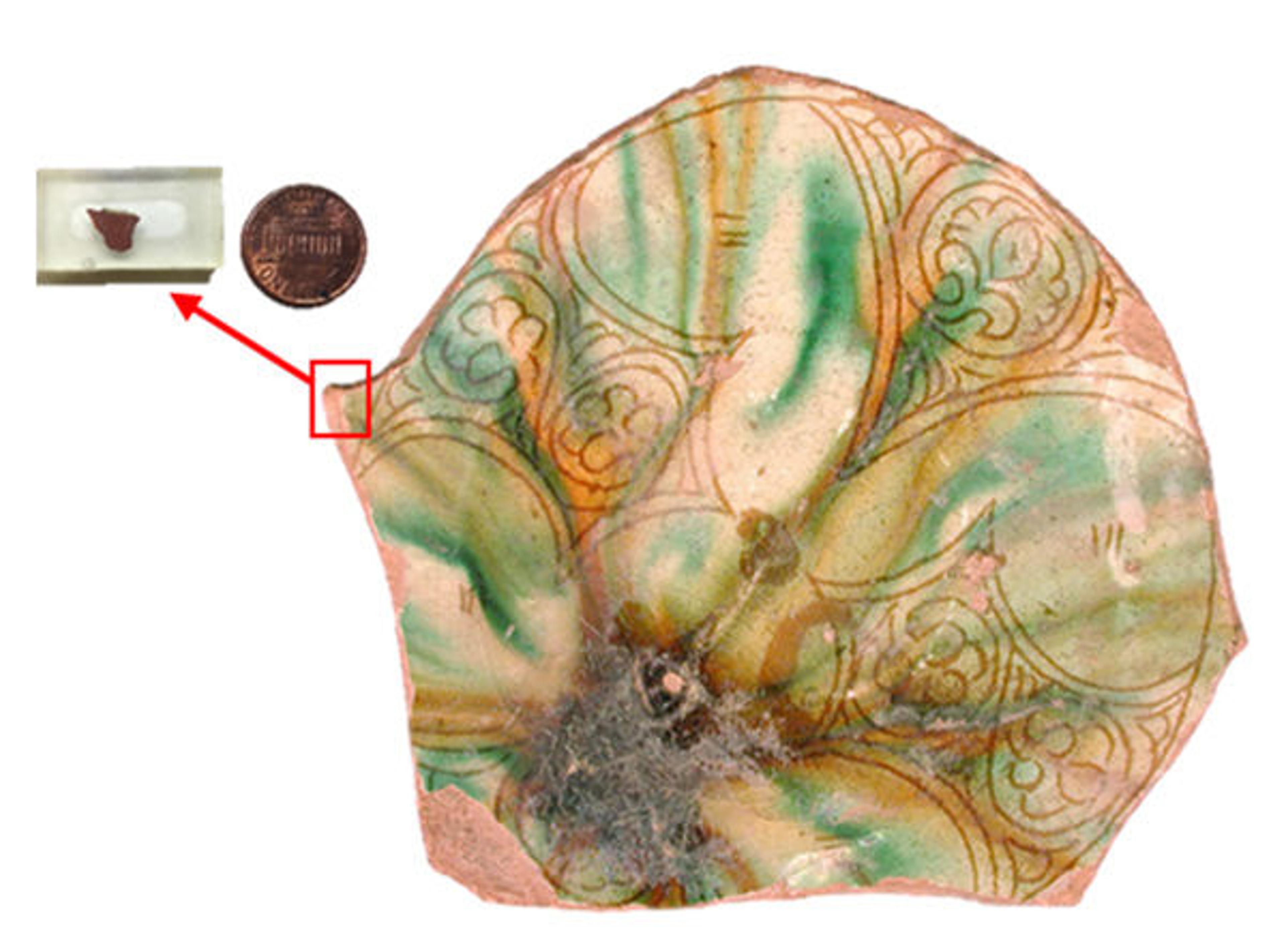
Fig. 2. Example of a sampling. A small sample is removed from a pottery shard, then embedded in a resin block, and its surface is carefully polished following a well-established procedure.
Making the Ceramic Body
These vessels were made on a wheel and shaped from a ceramic mass made of a fine-grained clayey material that is slightly rich in carbonate. The body also contains fragments of quartz, potassic feldspar minerals, and volcanic rocks. The nature of the mineral inclusions—including andesite, plagioclase, and quartz (determined by microscopic observations)—guided me to hypothesize that the ceramics were fabricated from a calcareous silt available in nearby Nishapur, in the fluvial deposits of the Nishapur plain (fig. 3).
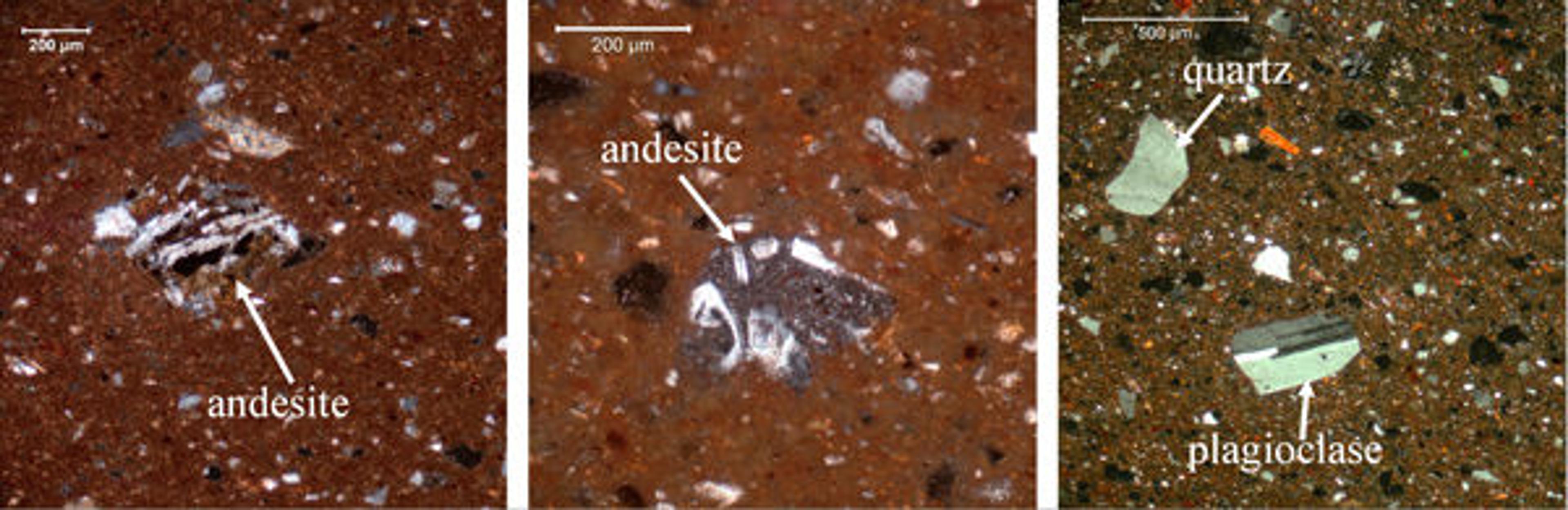
Fig. 3. Micrographs taken of thin sections of the ceramic body using a polarizing microscope, showing details invisible to the naked eye. A very thin slice of material, usually 0.03 mm thick, is placed on a glass slide between the objective lens of the microscope and a light source. When the light passes through the thin section, the different components, minerals and rock fragments, can be easily identified on the basis of their optical properties. In the above micrographs, the red/orange/brown background is the clay matrix and is composed by clay minerals transformed after firing.
Coating the Vessels
After the body of the vessels are formed, they are left to dry and, once leather-hard, coated with a white slip made of a mixture of quartz and feldspar minerals in a very fine kaolin-based material. The makeup of the slip was inferred by data taken from X-ray diffraction and a scanning electron microscope (SEM) (fig. 4). The slip material is made from the natural weathering of volcanic rocks such as rhyolites or granites. Such geological deposits do exist in Iran, but not in a reasonable distance from Nishapur, therefore suggesting that the industry would have relied on long-distance commerce for the gathering of some of its basic materials. In fact, there is a source dating to the beginning of the fourteenth century, Abu-l Qasim's treatise on ceramic production in Kashan, which describes a qamsarī stone as "a stone which once burned and broken up becomes a powder-like white sugar." Initially interpreted as dolomites or dolomitic limestone, the qamsarī stone might be instead a deposit of kaolinised granites that appears close to the Qamsar village, some 450 miles from Nishapur.
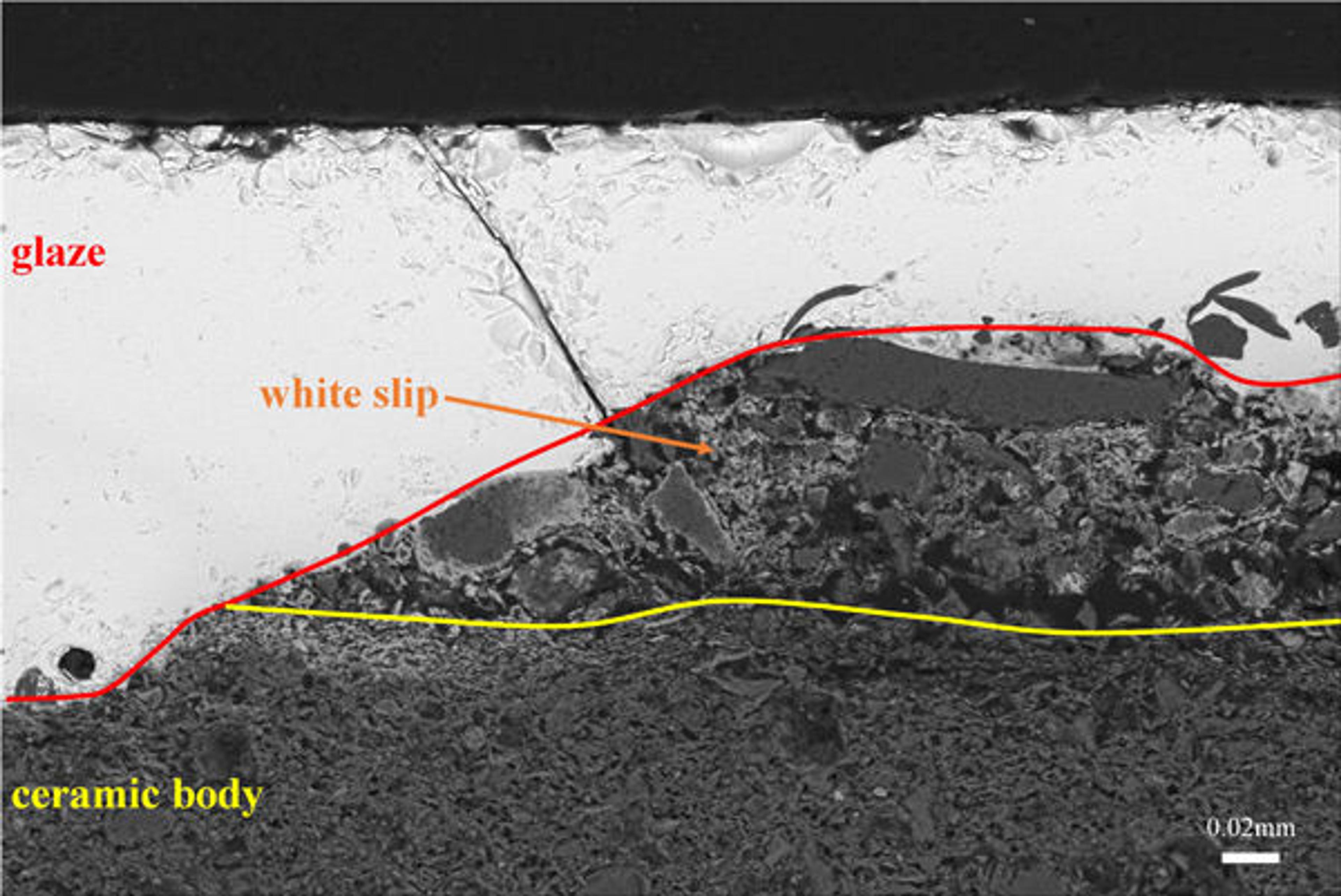
Fig. 4. SEM image showing the three main components of each sgraffito ware: the ceramic body, the white slip, and the glaze
Firing and Painting the Surface
After drying, the designs were scratched through the slip using a sharp tool to expose the reddish color of the clay, and the pots then underwent a first firing at a temperature around 1000–1050 °C. Colors, as metal-oxides in a water solution, were then splashed on the surface of the vessels and brushed alongside the lines of the scratched patterns.
Glazing and Second Firing
The vessels were then covered with a water solution of pure quartz and lead, which would have formed the transparent glaze after melting. The pots were piled up and separated by small, tripod-like stilts to prevent the melting glaze from sticking the pots together during the second firing at around 700–750 °C. It is very common to see some marks where the stilts came into contact with the pot surface (fig. 5).
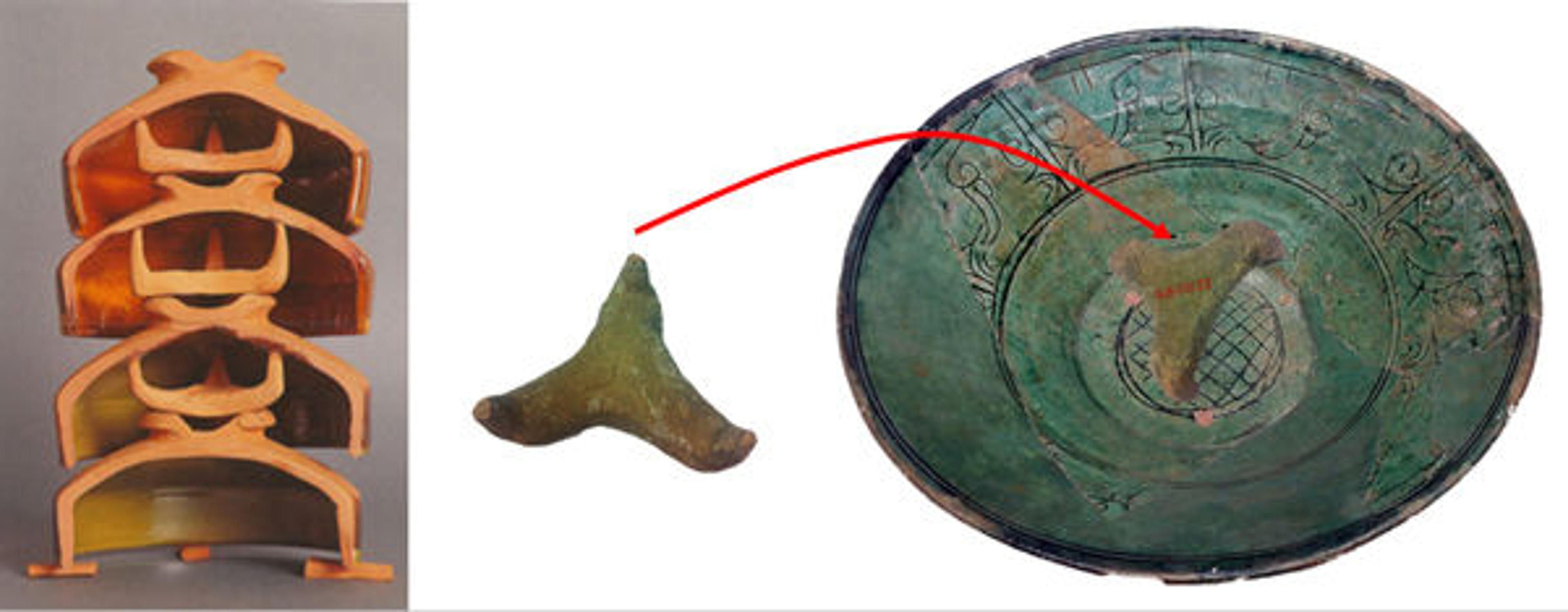
Fig. 5: Left: Modern reproduction of how bowls were stacked into each other. Photo courtesy of The Fitzwilliam Museum. Right: Example of how a stilt found at Nishapur perfectly fit into a partly reconstructed green monochrome bowl
The pigments used for the decorations would dissolve in the glaze, and their coloring chemical elements would be embedded into the glaze. It is normally impossible without such analyses to establish if a splashed decoration was executed before or after the application of the glaze, and the term "in-glaze" is used in these instances. Here, we have proven that the splashes were applied before the glaze.
Pigments
The composition of the pigments was investigated by combining elemental compositions measured by X-ray fluorescence and SEM-EDS microanalyses: iron oxides were used to create orange and brownish-yellow colors; chrome-spinel for greenish-yellow; copper for green colors; manganese oxides and silicates for purple and black colors. The greenish chrome-based yellow, apparently used only in Nishapur production, anticipated the prominent use of chrome yellow in eighteenth-century Europe. Monochrome green vessels were covered with a colored glaze obtained with copper green, and were not underglaze splashed. All the pigments identified in the Nishapur sgraffito pottery could be easily found in rocks not far from the site.
There is a lot more to know about the sgraffito ware from Nishapur and its production technology, so stay tuned! The results of my research will be published soon in a scientific journal.
Related Links
Learn more about Conservation and Scientific Research Fellowships at the Met.
View all blog posts related to the Department of Scientific Research.
Elena Basso
Elena Basso is an Associate Research Scientist in the Department of Scientific Research.