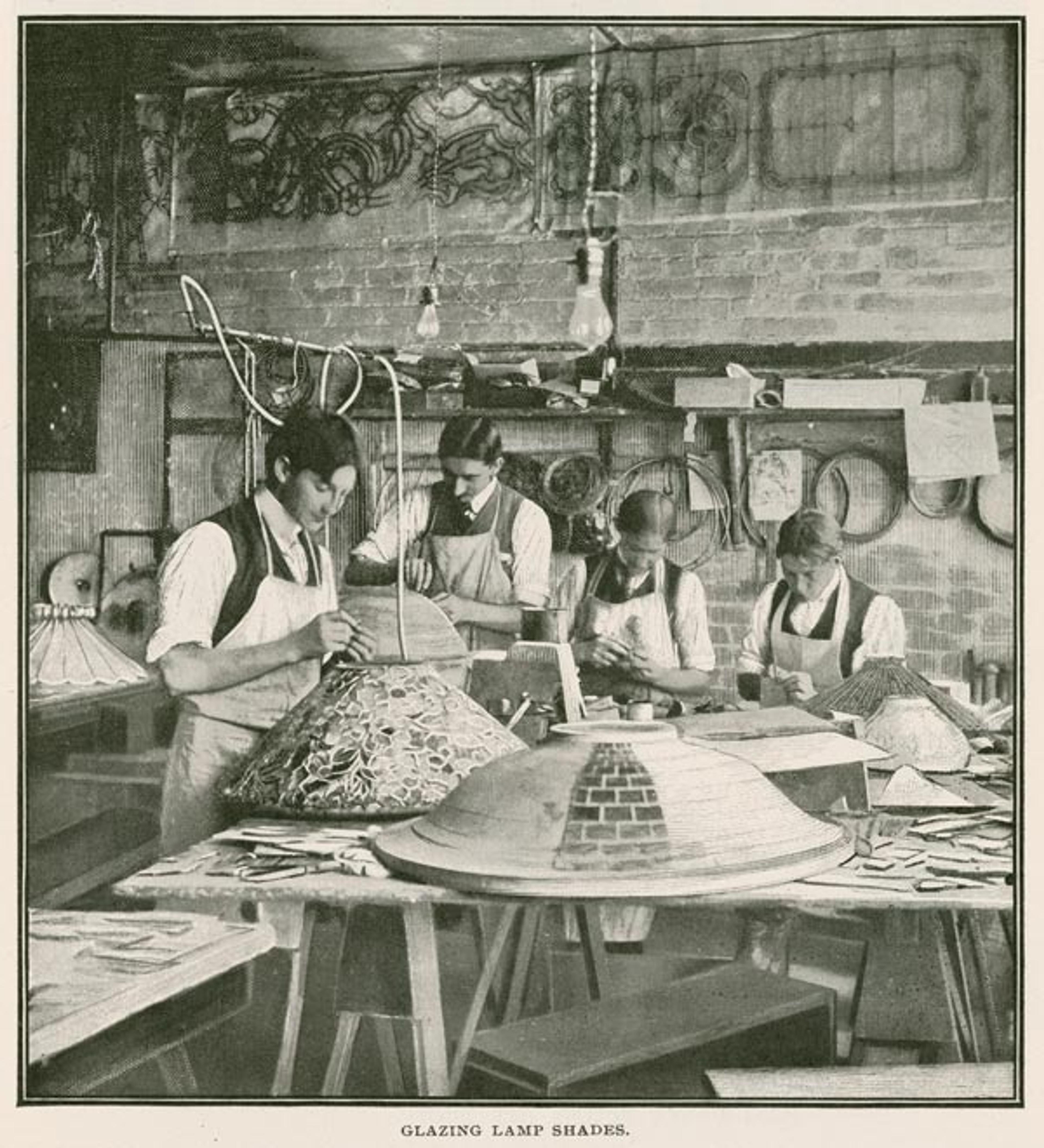
Workers in the Tiffany Studios lamp department ca. 1898, from The Cosmopolitan: A Monthly Illustrated Magazine, January 1899
«Have you ever viewed an artwork and wondered how it was made? The Met's collection is full of art that inspires us to ponder its creation, but the Museum rarely reveals the many steps that were taken to create the final work of art.»
Some of the questions that often come to mind when walking through the galleries include: Who made this? What is it made of? How was it made? How long did it take? A small installation in gallery 774 aims to highlight the processes and tools that were used either to reproduce or create two important works in our collection: Tiffany & Co.'s 1875 masterwork, The Bryant Vase, a birthday gift for the journalist and poet William Cullen Bryant; and Tiffany Studios' leaded glass lampshade for the "Tulip" lamp.
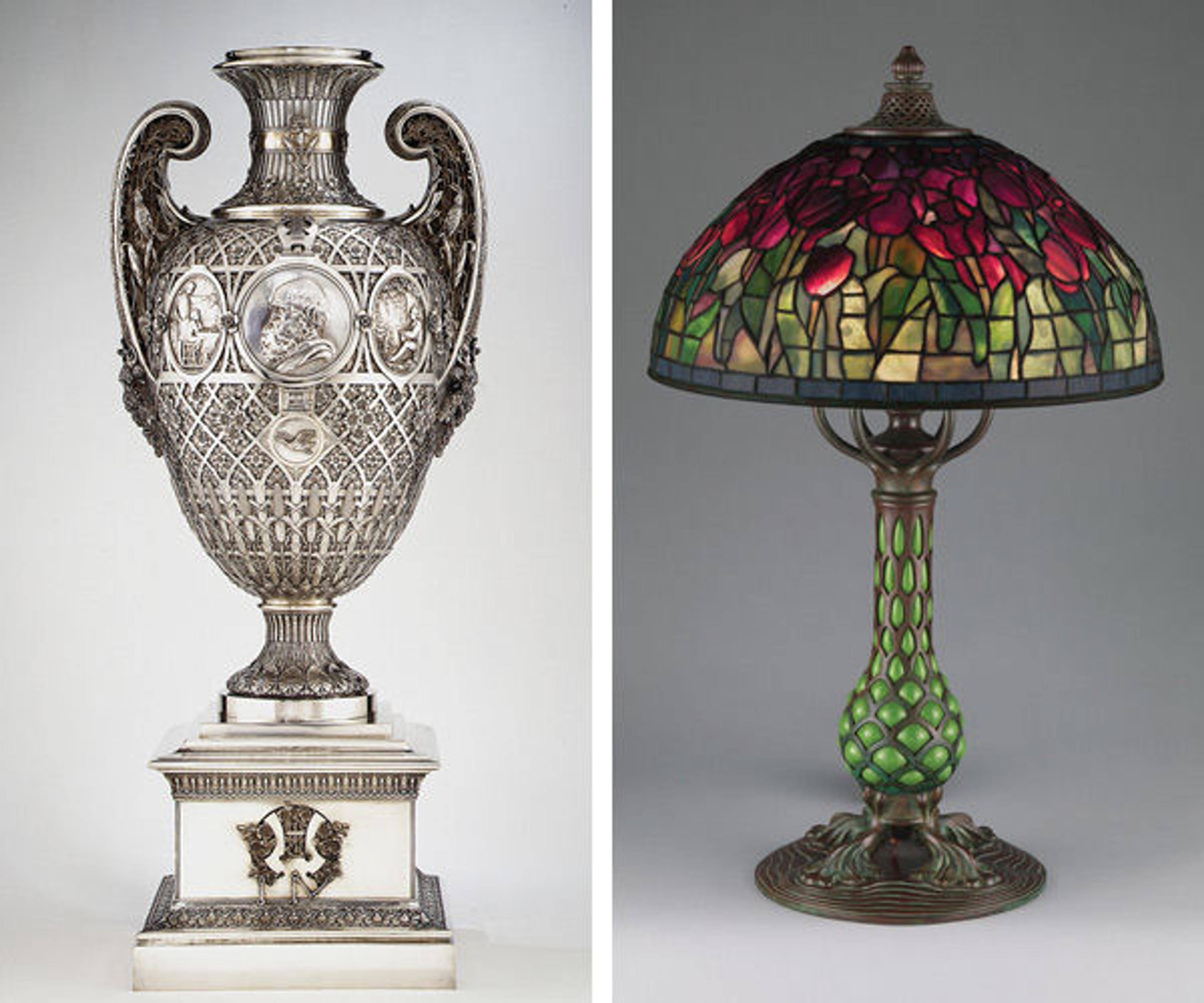
Left: The Bryant Vase, 1875–76. Manufactured by Tiffany & Co. (1837–present). American. Silver; 33 1/2 x 14 x 11 5/16 in. (85.1 x 35.6 x 28.7 cm); diam. 11 5/16 in. (28.7cm); 452 oz. 16 dwt. (14084.2 g). The Metropolitan Museum of Art, New York, Gift of William Cullen Bryant, 1877. Right: "Tulip" lamp, 1907–12. Tiffany Studios (1902–32). Leaded Favrile glass and patinated bronze with a reticulated blown glass base; 23 1/8 in. (58.7 cm); body diameter: 14 in. (35.6 cm). The Metropolitan Museum of Art, New York, Gift of Mr. and Mrs. Richard L. Chilton Jr., 2011 (2011.99.3)
The installation features the molds that were used to replicate The Bryant Vase through a process called electrotyping, and an accompanying video illustrates this complex and fascinating technique. Scientifically inclined visitors might find it interesting that electricity and charged ions are central to this process.
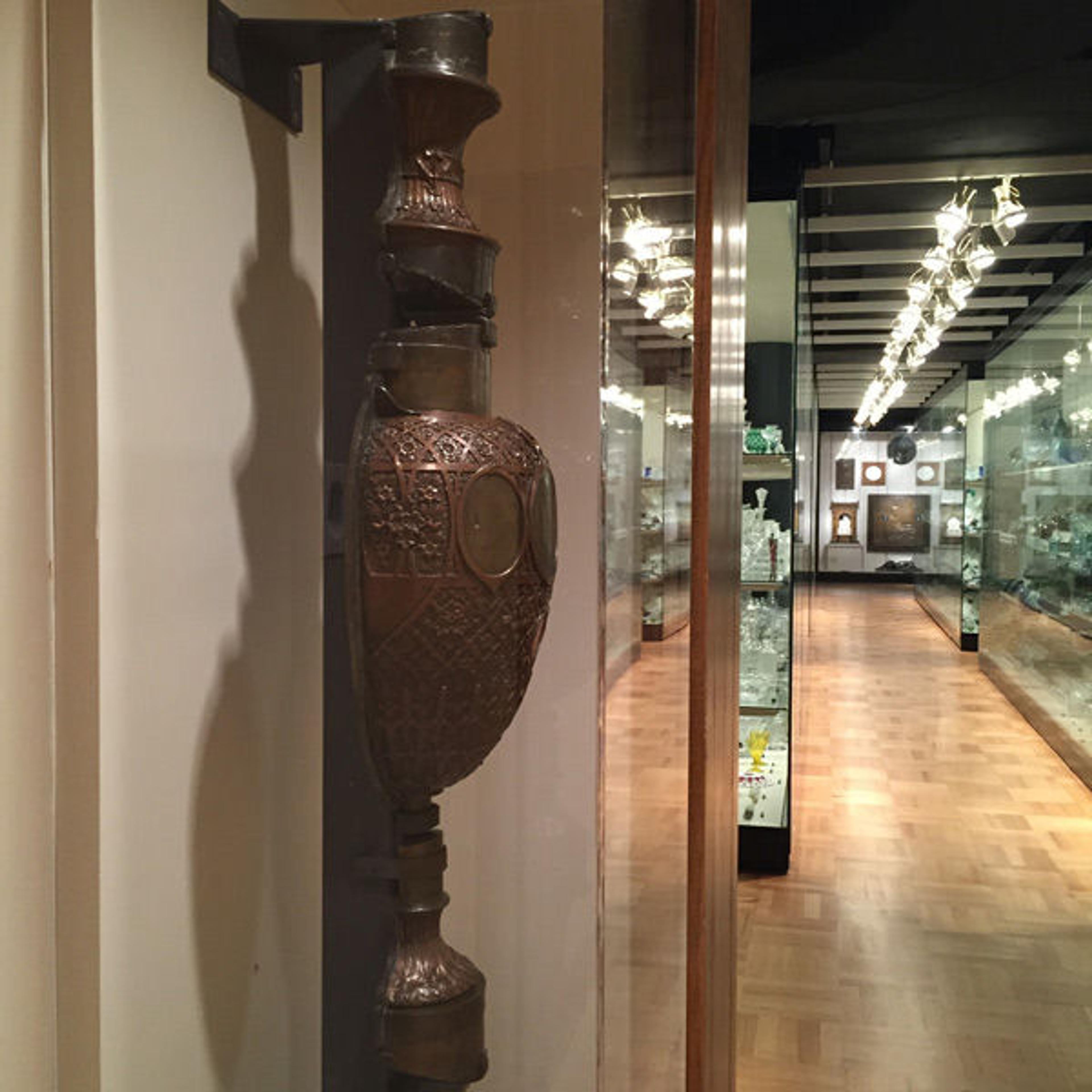
A mold used to replicate The Bryant Vase, on display in gallery 774
Nearby, the workbench and tools utilized by John Dikeman—the last head of the Tiffany Studios lampshade shop—help us to visualize the studio in which Tiffany lamps were produced.

John Dikeman at his work bench, Tiffany Studios, 1921. Photograph, Department of American Art, The Metropolitan Museum of Art
Long before any pieces of glass were cut and assembled on a wooden mold, like the one Dikeman is leaning on in the photograph above, an approved watercolor design of the shade was translated into a cartoon and sample pattern, which suggested a color for each piece of glass.
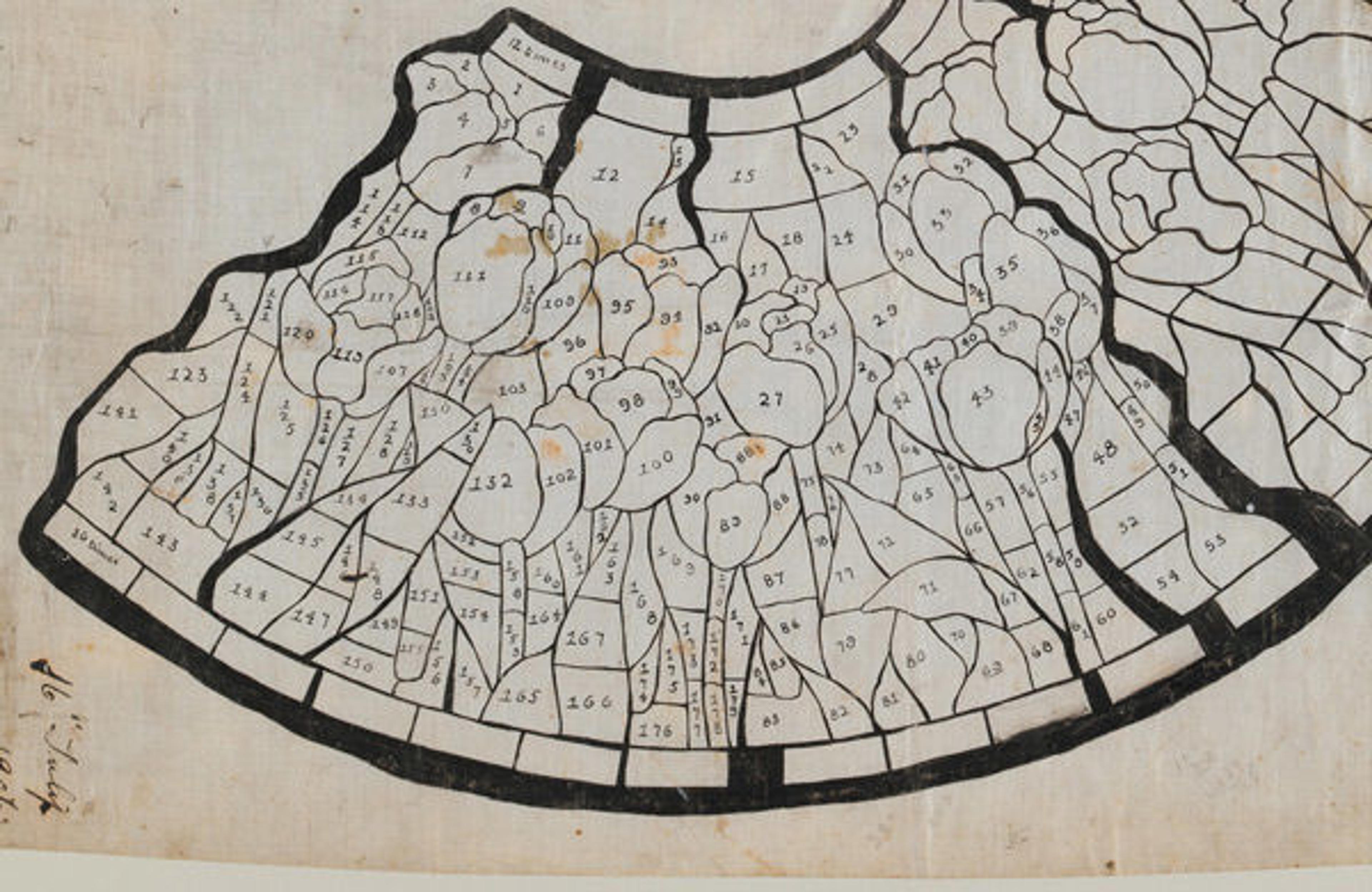
Notice how the cartoon is numbered; these numbers correspond to the individual cardboard or brass templates used to cut the glass. Louis Comfort Tiffany (American, 1848–1933). Cartoon for tulip shade, ca. 1906. Tiffany Studios (1902–32). Ink on glazed fabric; 25 1/4 x 29 1/2 in. (64.1 x 74.9 cm). The Metropolitan Museum of Art, New York, Gift of Fred and Nancylee Dikeman, in memory of his father, John Dikeman, 1980 (1980.497.14)
An artist, usually a woman, was responsible for the selection and cutting of glass, and a craftsman, most likely a man, was in charge of soldering the pieces together.
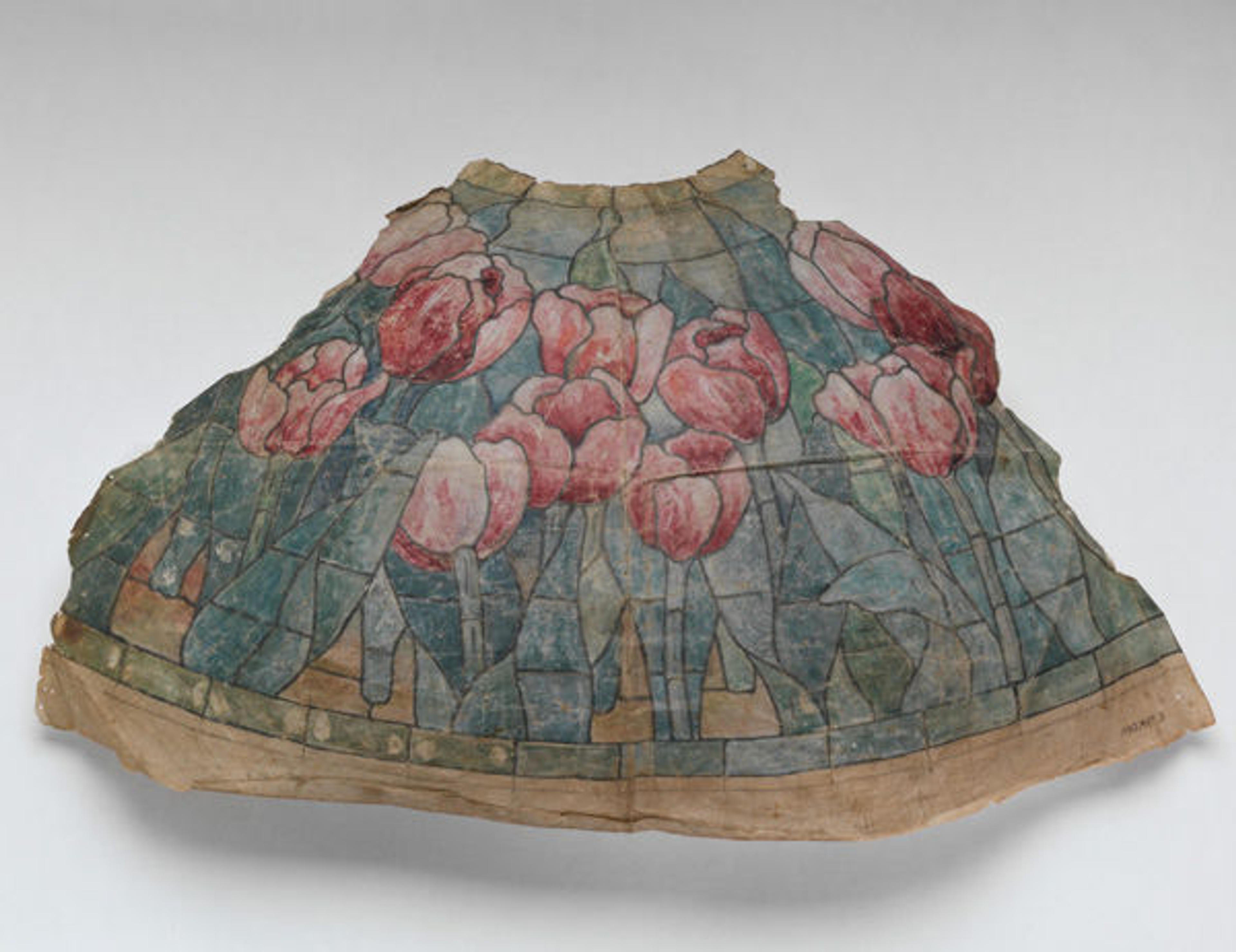
Sample pattern for a lamp shade, 1900–1907. Tiffany Studios (1902–32). American. Metal, cloth, glass; a: 9 1/2 x 16 1/16 in. (24.1 x 40.8 cm); b: 9 9/16 x 5 1/2 in. (24.3 x 14 cm). The Metropolitan Museum of Art, New York, Gift of Fred and Nancylee Dikeman, in memory of his father, John Dikeman, 1980 (1980.497.5)
We hope that shedding some light on the process of how these artworks were made will make them even more interesting. Come and see it for yourself!